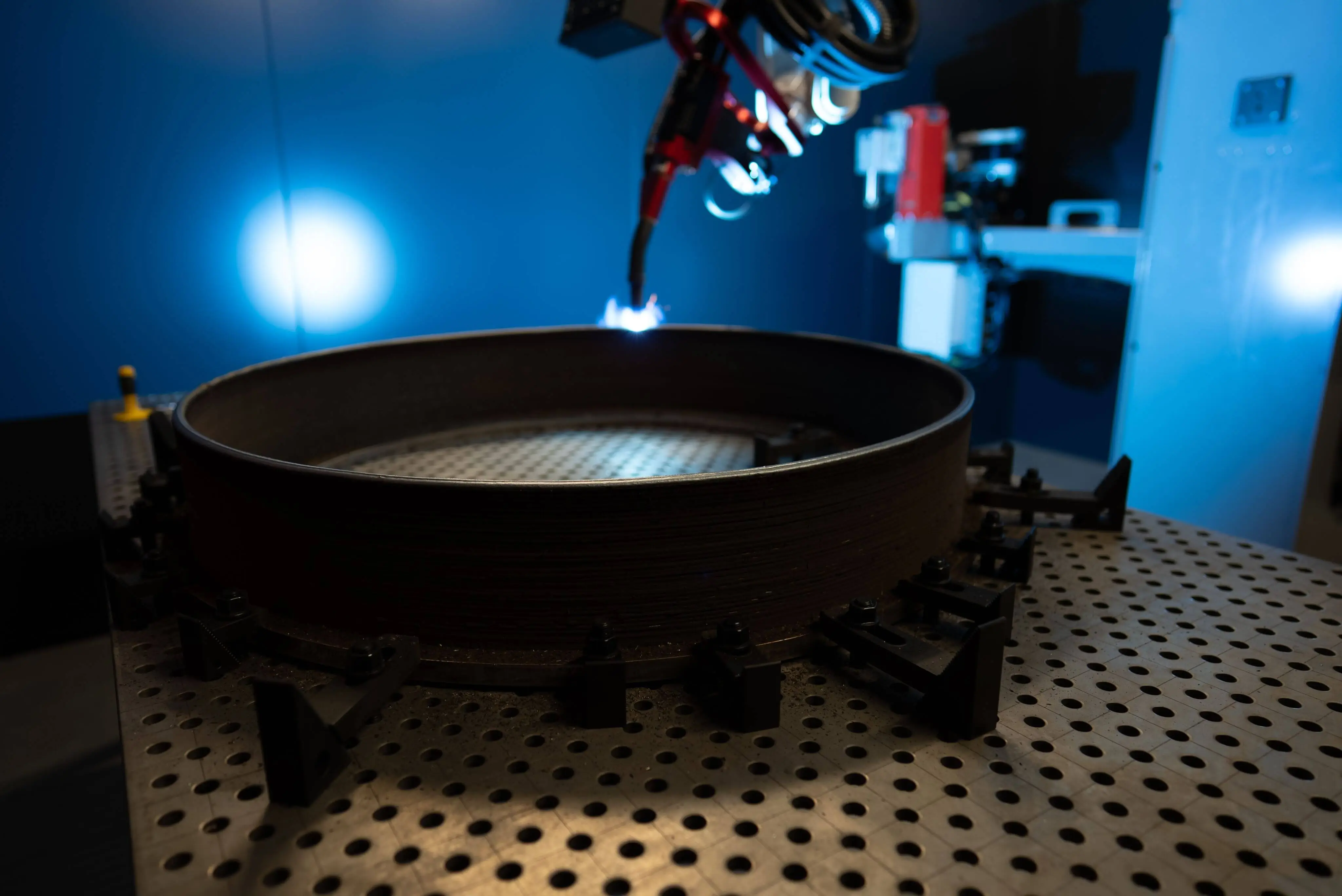
Redefining what's possible in large-scale component manufacturing
We manufacture large and ultra large-scale component parts using our 20 Wire Arc Additive Manufacturing (WAAM) systems and the supporting infrastructure around them.
Single-arm production volume is up to 2.8 metres in diameter, 3.2 metres in height.
Multi-arm production volume, through the revolutionary HexBot, is up to 6.2 metres in diameter, 3.2 metres in height.
Our capability is ideal for multiple industries where there is demand to produce low volumes of large-scale metal component parts, including maritime, offshore and other energy sectors.
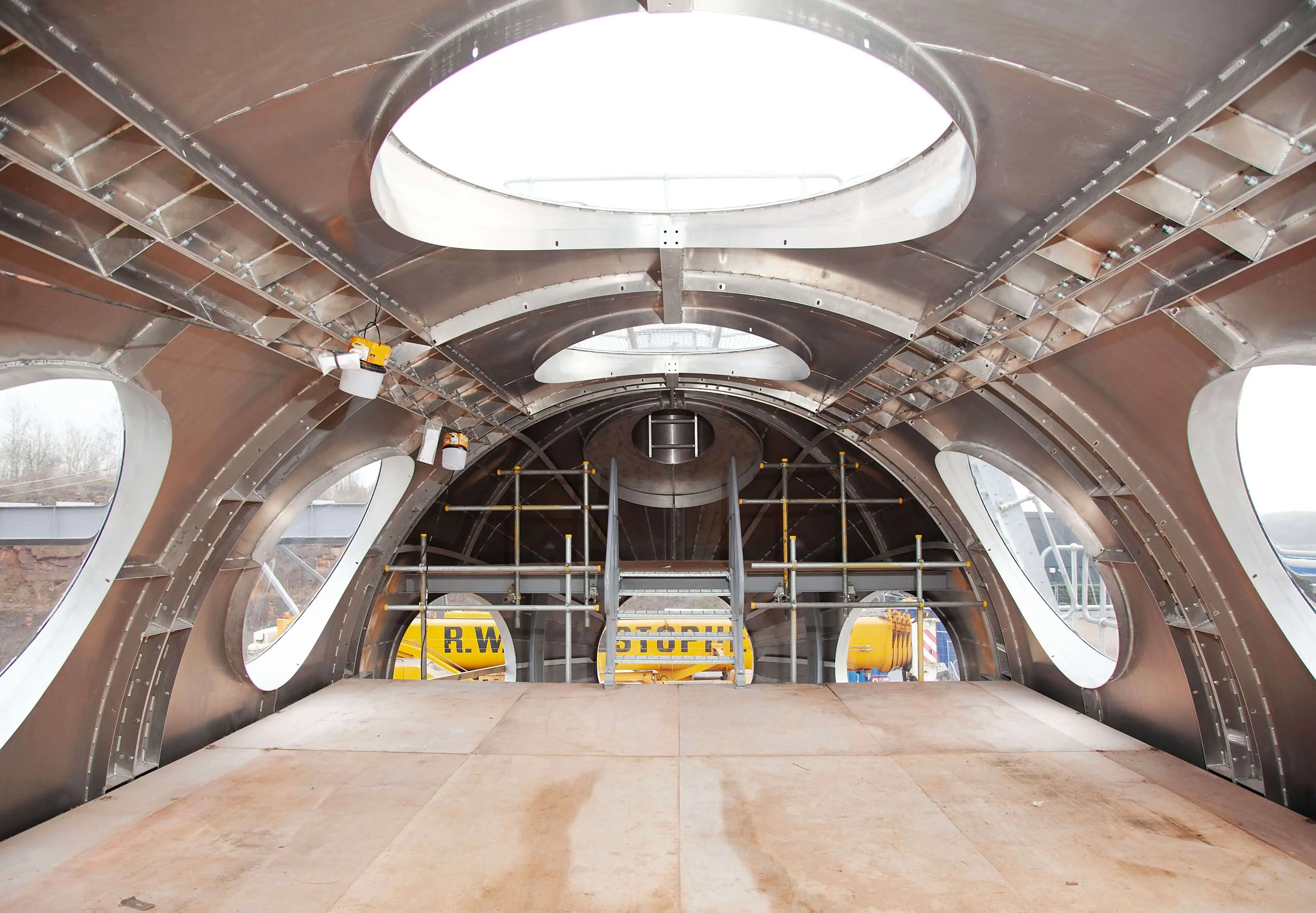
Producing component parts to the highest standards
We adhere to the highest industry standards and certifications.
We work closely with DNV, one of the world’s leading classification societies, to put in place the highest levels of assurance in our output and procedures.
Procedures, facilities and operations are approved to DNV standards. Our Quality Management Systems are approved to ISO 9001 standard.
We undertake the material and product certification of the components we produce, rather than placing this burden on our clients. This process, and the standards to validate outputs, are to the same standards as a traditionally manufactured component.
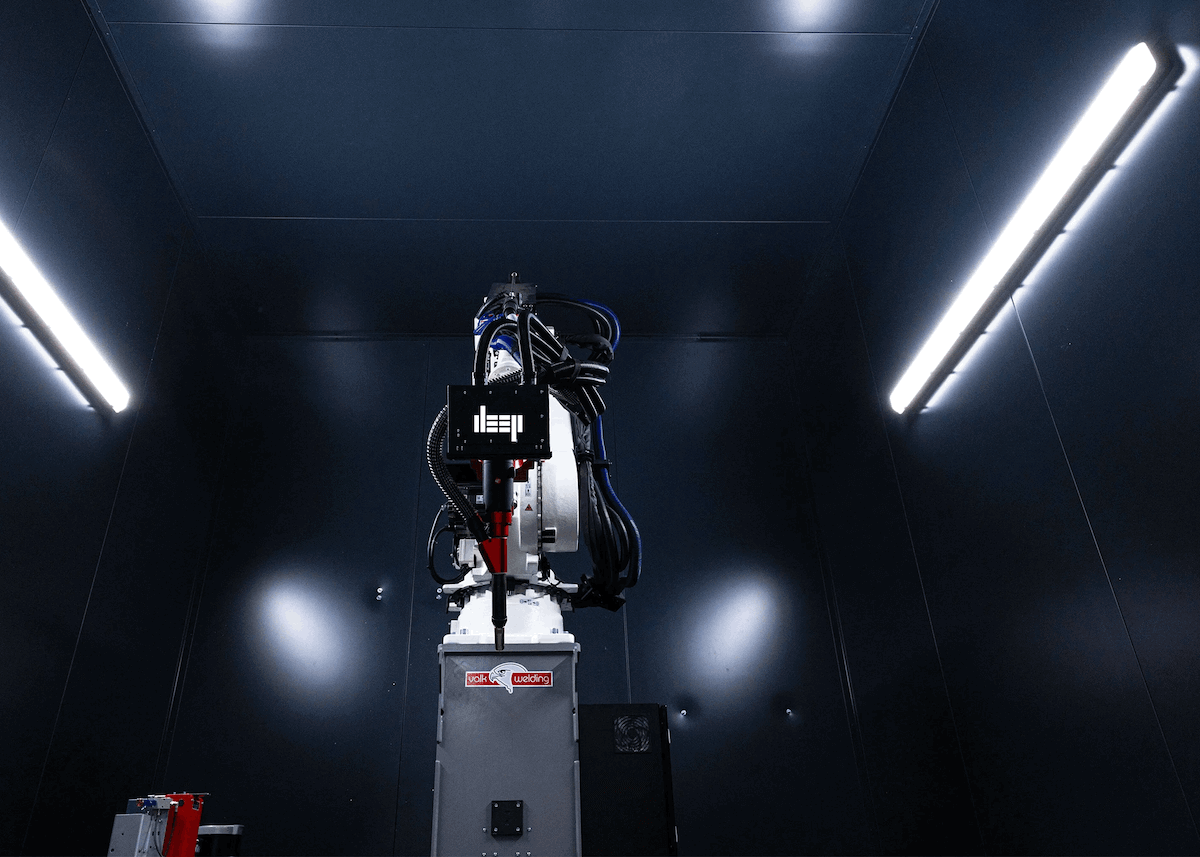
Reducing the production timeline for component parts
One reason why we invested in Wire Arc Additive Manufacturing (WAAM) is because of its ability to significantly reduce lead times.
Production timelines for large component parts can be cut by more than half compared to traditional methods like forging or casting.
We automate our operations and can run our facility 24/7, further increasing the speed of delivery and capacity we offer.